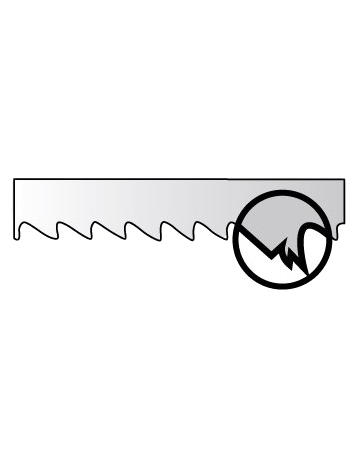
Bandsaw Gullet Cracking
Cause: The gullet area (the space between the teeth) can crack due to a variety of factors. Common causes include issues with guides, tension, feed rate, coolant, speed, bearings, and welding.
Key Factors & Solutions:
- Guides Too Tight
- Issue: Excessive side pressure from tight guides restricts blade movement, causing the blade to stretch.
- Effect: The tension creates stress on the gullet, which leads to cracks.
- Solution: Adjust guides to ensure minimal side pressure, allowing the blade to run smoothly.
- Tension Too High
- Issue: Excessive tension on the blade causes the flexible backing to stretch, while the rigid teeth resist.
- Effect: This results in uneven stress on the gullet and cracking.
- Solution: Reduce the blade tension to ensure the blade maintains flexibility and reduces over-stretching.
- Feed Rate Too Heavy
- Issue: A high feed rate pushes material too quickly into the blade.
- Effect: The gullet area fills too quickly, preventing the teeth from exiting the material properly, leading to pressure and damage.
- Solution: Reduce the feed rate to allow the teeth to clear the material more effectively.
- Coolant Flow Too Low
- Issue: Insufficient coolant causes rough cutting due to a lack of cooling.
- Effect: The blade temperature rises, which can cause heat-related damage, especially to HSS teeth.
- Solution: Ensure adequate coolant flow to maintain proper cooling during operation.
- Improper Coolant Mixture
- Issue: An improper coolant concentration reduces cooling efficiency.
- Effect: Insufficient coolant leads to heat build-up, increasing blade wear.
- Solution: Use the correct coolant dilution (e.g., 1:20 for steel, 1:10 for stainless steel) based on the material being cut.
- No Need for Coolant (for Certain Materials)
- Issue: Materials like SpK alloy steel and cast iron have low friction and don’t require coolant.
- Effect: Coolant may cause the blade to slip, leading to damage.
- Solution: Avoid using coolant for such materials, and instead, reduce the blade speed to manage heat.
- Speed Too Fast
- Issue: Cutting too fast with hard materials (like stainless steel) increases blade wear.
- Effect: Excessive speed leads to blade damage, gullet cracking, and premature wear.
- Solution: Slow down the cutting speed to minimize wear, especially for harder materials.
- Broken Guide Bearings
- Issue: Vertical guide bearings help keep the blade aligned. If damaged, the blade can wobble.
- Effect: Wobbling leads to erratic cutting and increases the risk of blade breakage.
- Solution: Inspect and replace any worn or damaged guide bearings to ensure proper blade alignment.
- Jumping or Shaking Machine Head
- Issue: Shaking or jumping can be caused by:
- Damaged guide bearings
- Misaligned blade welding
- Hydraulic system defects
- Effect: These vibrations cause stress on the blade, leading to cracks and other failures.
- Solution: Replace damaged bearings, re-align the blade during welding, and inspect the hydraulic system for leaks or failures.
- Issue: Shaking or jumping can be caused by:
- Gullet Welding (for Certain Materials)
- Issue: Materials like aluminum can stick to the gullet.
- Effect: This buildup reduces the blade’s effectiveness and increases wear.
- Solution: Use a brush or increase coolant flow to clean the gullet and prevent material buildup.